There are a lot of data-driven maintenance strategies, how do you know which one is right for you and your assets? How do you know if any are even better than simple preventative maintenance or no proactive strategy at all?!
In this article, I will provide an overview of the following 5 types of maintenance using lots of graphics:
- Reactive Maintenance
- Preventative Maintenance (PM)
- Condition-Based Maintenance (CBM)
- Predictive Maintenance (PdM)
- Prescriptive Maintenance
As you can see, there's a lot to cover in this post!:
- Types of Maintenance
- Cost and ROI
- Picking a Maintenance Strategy Based on Machine Asset Type
- How to Get Started with Prescriptive Maintenance- Exploration!
- Conclusion and Additional Resources
Types of Maintenance
P-F Curve of Different Types of Maintenance
To define and understand the difference between these types of maintenance, let's first look at a P-F curve which starts with a potential failure (P) and ends with a functional failure (F).
Reactive maintenance waits for the system to experience a functional failure before maintenance occurs, so this doesn't even appear on the P-F curve.
Preventative maintenance performs maintenance on some fixed schedule ideally aligned to be slightly shorter than the typical P-F interval for a particular machine. This will ideally let it catch a system while it is in the middle of the curve. The trouble is that the equipment may deteriorate too fast for the preventative maintenance schedule to correct it in time. Or, the preventative maintenance may be wasteful if it is "fixing" a perfectly fine piece of equipment.
Condition-based maintenance uses sensors and data with preset conditions or thresholds that when met will signal maintenance is needed. The trouble is that this requires a fairly noticeable amount of degradation to have taken place in order to hit these thresholds.
Predictive maintenance uses sensors and data to detect trends in the health of a system and predict when failure will occur. This allows it to detect the deterioration of a machine earlier than CBM and allows maintenance teams more time to schedule maintenance at a convenient time, knowing when the PdM predicted failure to occur.
Prescriptive Maintenance uses sensors, data, and advanced analytics to determine the route cause of a potential failure so specific corrective action can be prescribed. The advanced data and analytics needed for successful prescriptive maintenance also ensures the potential failure is identified even earlier which makes fixing the problem easier and less expensive.
Evolution of Maintenance Based on Data
Another way to look at the difference between maintenance types is to understand their dependence on data. This is the most defining distinction between these maintenance strategies.
Reactive maintenance has absolutely no dependence on data, it waits for failure.
Preventative maintenance uses either time or usage to inform its maintenance schedule, it's not a lot of data - but it's a start!
Condition-based maintenance will typically look at a single metric and check against preset thresholds.
Predictive maintenance typically looks at a handful of data sets and relies on slightly better analytics to pick up on various trends in the data and the health of the asset.
Prescriptive maintenance uses many data sets and metrics and likely some proprietary analysis techniques to determine the root cause of a potential failure.
Now that we've given a good overview of the different maintenance strategies, let's dive a bit deeper into each one.
Reactive Maintenance
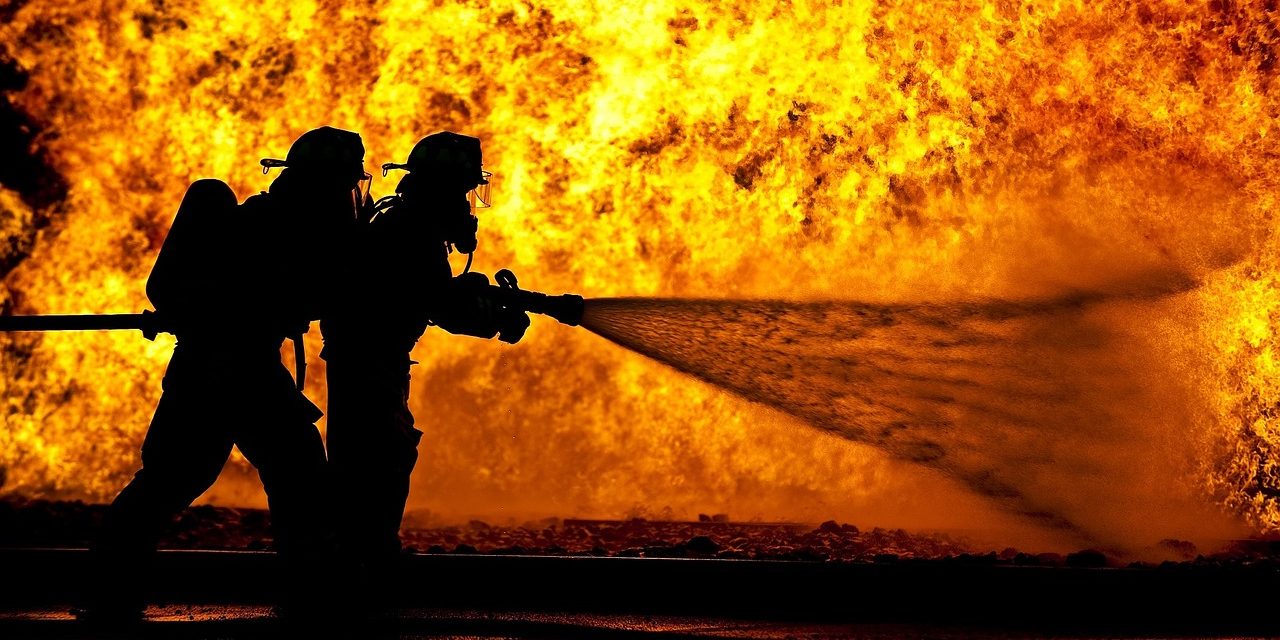
Reactive maintenance is just as it sounds: wait until the machine fails and then fix it. In general, this is often not really a maintenance strategy -- it is often the result of having no strategy at all. Once the machine goes down, the team scrambles trying to find a fix and they feel like they are constantly putting out fires!
There is an exception, though, when you can make reactive maintenance an actual strategy that has some value. If your machines are:
- Easily fixable
- Replacement parts are readily available
- Downtime is not costly, there are redundant machines
Then a reactive maintenance strategy can be a good idea assuming you are planning for this and it is not costly in both time and money. This is called a "Run to Failure" strategy.
Benefits and Pros of Reactive Maintenance
- No up front cost or cost to manage
- Minimal maintenance staff needed
Downsides and Cons of Reactive Maintenance
- Unpredictable and inconsistent downtime
- High costs associated with fixing a failed machine
- Repairs tend to be urgent which may require overtime labor
Preventative Maintenance (PM)

Preventive maintenance is using some routine, either time or usage, to define when you replace or rework some components of your system. An example of this is how you replace the oil in your car every 5,000 miles.
This is a good idea to prevent any deterioration in the machine from occurring in the first place. It is easier to plan and work around and it's also generally less expensive to replace a simple component a few times than repairing a damaged machine after failure. But this has a few notable issues:
- Schedule may be too frequent - you may be paying for maintenance on a perfectly healthy machine, which is wasteful in labor and parts
- Schedule may be too infrequent - your maintenance window may miss a rapidly accelerating failure
- Lulled into a sense of security, failure may arise from another cause - the preventative maintenance can only address the common failure modes; replacing your oil won't prevent a belt failure, for example
The more complex your machine is, the more unlikely preventative maintenance will be a feasible maintenance strategy. This is because it will require too many different things to maintain (all at different rates) making it probable that one of those things were excessively fixed (wasteful) or that a failure was missed altogether.
Benefits and Pros of Preventative Maintenance
- Increases asset life span
- Reduces unplanned downtime
- More efficient use of energy and resources
Drawbacks and Cons of Preventative Maintenance
- Schedule may be too frequent (wasteful)
- Schedule may be too infrequent (misses a potential failure)
- Can't catch uncommon failure modes
Condition-Based Maintenance (CBM)
Condition-based maintenance uses sensors mounted to a machine to periodically check the health of that asset. Then it compares the most recently measured value against preset "conditions" to be reached which signify an alarm or warning. Typically this is done by:
- Establishing a baseline of a known good or healthy machine
- Calculate a normal distribution of the data taken
- Set warning levels at +/- 3 standard deviations and then alarms at +/- 5 standard deviations off the baseline levels
In the example below, about 70 hours into the profile the velocity RMS (a common vibration metric to use) on this machine reaches the warning level which a condition-based maintenance system could detect and report.

Benefits and Pros of Condition-Based Maintenance
- Increases asset life span
- Real-time (and often remote) indication of the health of an asset
- Maintenance only performed when needed
- Advanced warning provided to allow for convenient scheduling of maintenance
Drawbacks and Cons of Condition-Based Maintenance
- Requires monitoring hardware and software to generate warnings which have upfront and recurring costs
- Some software may require the user to be specially trained to operate
Predictive Maintenance (PdM)
In the example above about condition-based maintenance, there was clearly a trend in the data before it reached the warning level. This trend is exactly what a more advanced algorithm would be able to detect and is more accurately considered "predictive." Predictive would then go that added step further and predict how much usable time remains in the asset to schedule maintenance -- it predicts when failure will occur.
Predictive maintenance (PdM) is not magic; it is about measuring one or many parameters and using this data to make an informed prediction about how the health of the machine will look in the near future.
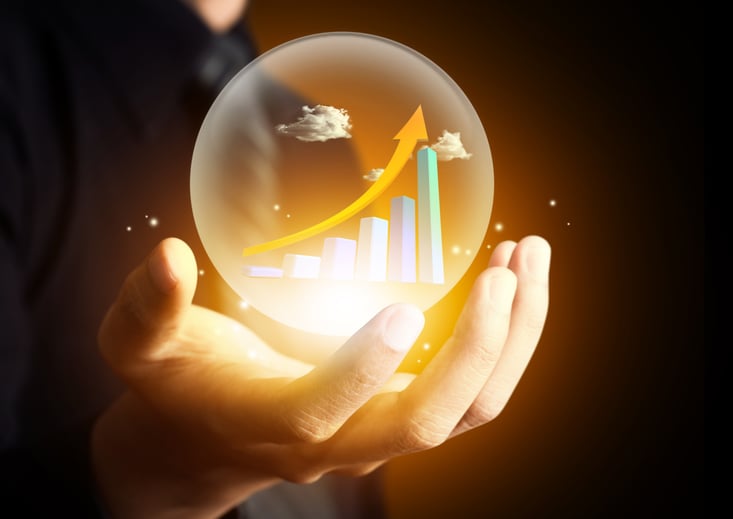
In order to have this data-driven crystal ball, predictive maintenance solutions typically require more & better data as well as advanced analytics compared to CBM solutions. And this will often require some machine learning algorithms to be effective.
Benefits and Pros of Predictive Maintenance
- Increases asset life span
- Real-time indication of the health of an asset
- Maintenance only performed when needed
- Advanced warning provided to allow for convenient scheduling of maintenance
Drawbacks and Cons of Predictive Maintenance
- Requires monitoring hardware and software to generate warnings which have upfront and recurring costs
- Some software may require the user to be specially trained to operate
Prescriptive Maintenance
In order to have a prescriptive maintenance program, you need to be able to correlate specific signatures in the raw data and trends to specific root causes. And this tends to require you to have been able to previously find these signatures after the fact.
Let's look at an example from the US Navy using enDAQ sensors detailed in this case study. The US Navy begins seeing a rise in physiological episodes that put crewman and aircraft at risk -- this was both a safety and financial risk [see news article]. Physiological episodes were manifesting as pilot hypoxia symptoms thought to be a result of cockpit air contamination, lack of oxygen, or issues with the Environmental Control System (ECS).

They responded to this issue by:
- The US Navy needed data to determine the root cause of the physiological episodes and turned to enDAQ, a convenient, adaptable and flight qualified data acquisition system (originally developed for vibration, but also included other sensors such as pressure) to measure pressure inside the cockpit.
- The US Navy began measuring the pressure profile of EVERY F-18 flight of the Navy around the world -- that is a lot of data!
- Data was first used to identify when there was an episode and help treat the pilot -- first using condition based maintenance.
- But then data scientists began looking back in the data in search of indicators that could have predicted the event -- now using predictive maintenance
- And with even more data, scientists started to be able find more intricate signatures to tell maintenance teams which specific part to fix -- evolved into prescriptive maintenance
- This is what is pictured in the image above showing the table of metrics (that correspond) to various components within the environmental control system and particular operating states during the flight.
- Looking at this data (the data has been modified from its original form for security reasons), the Navy is able to make maintenance decisions and inform their crew what particular parts need to be fixed.
To quote the Rear Admiral Fredrick Luchtman:
“...we are almost to the point with our data analytics where we receive information from the fleet, we analyze that information, and then we can tell the fleet, hey this particular aircraft is exhibiting signs that this particular part may be needing to be replaced pretty soon.”
This quote and example is especially import to highlight that prescriptive maintenance (and predictive for that manner) requires an evolution: You start by being in a state where you have a problem and are reacting to failures. Then you begin doing some preventative maintenance to and in that may start periodically gathering data. This data can then start being used as a condition-monitoring program. With more time and more data, you may have enough to start being able to use that to predict failure. And with even more data you begin being able to find root causes and prescribe the specific corrective action ahead of time. It's an evolution, so let's revisit that earlier image!
Cost and Return on Investment (ROI)
When looking at the cost of a maintenance strategy, there will be a few considerations:
- Labor
- Recurring: Time spent by maintenance personnel to execute the strategy on a daily basis
- One-Time: Training to understand the maintenance equipment & software (if any)
- Monitoring Equipment & Software (if any)
- Recurring: Software charges to license the analytics and alerting capabilities
- One-Time: Purchasing and installing the sensors used as the data source
These maintenance investments will (hopefully) have a return on said investment in the form of:
- Reduced cost of repairs: This is because preventative and predictive maintenance strategies are generally fixing something "small" before it turns into a catastrophic and expensive failure.
- Increased Asset Uptime: Machines are running only if they are generating a profit which means if a machine is down due to a failure you have an opportunity cost because it isn't making money.
The plot below compares our maintenance strategies and illustrates how they stack up on that return on investment.

- Reactive Maintenance
- No cost to install and manage because you're doing nothing!
- But it also is going to have the highest cost of repairs because it requires fixing catastrophically failed machines and doing so urgently. And this strategy is likely to have machines down for longer periods of time. But as we'll see in the next section, there are some times this still makes sense.
- Preventative Maintenance
- Linear/proportional increase in both cost & savings
- It has a big jump up in costs to manage because you will now be paying people to perform maintenance on a schedule and paying for these parts and material needed in the smaller maintenance tasks.
- But this comes with a proportional increase in savings from both cost of repairs and increased machine uptime. The preventative maintenance will without a doubt reduce the likelihood of failure and downtime while also generally having cheaper repair costs as it replaces inexpensive components.
- Condition-Based Maintenance
- Slightly higher increase in savings relative to costs
- Condition-based maintenance requires some upfront investment in the monitoring equipment and training. It also generally will have some recurring cost associated with software licenses and paying people to pay attention to the data and alarms (and some require humans to manually capture the data).
- But you will have a slightly higher proportional increase in savings as you ensure repair costs are only allocated to machines in need of it. And this will provide greater peace of mind (rightfully so) that you won't have unexpected downtime of a machine providing greater savings.
- Predictive Maintenance
- Higher increase in savings relative to cost increase
- If you already have a condition-based maintenance strategy then the only increase in costs will be for better & more data, and better analytics, which is relatively small to the initial investment for CBM in the first place.
- But predictive maintenance will further increase machine uptime as failures can be predicted and maintenance scheduled conveniently. Costs will also generally be less because the failure was caught even earlier.
- Prescriptive Maintenance
- Much higher increase in savings relative to cost increase
- Like the difference between CBM and PdM, the step up in costs from preventative to prescriptive is also relatively small - again only for better & more data with better analytics. But the most important thing it needs relative to predictive is just even MORE data and history, which isn't all that expensive.
- Prescriptive maintenance offers a massive increase in savings however as you are able to tell maintenance teams exactly what to fix (and what parts to bring with them) without needing them to do onsite evaluations. This also will provide even further improved machine uptime as failures are detected even earlier.
Picking a Maintenance Strategy Based on Machine Asset Type
There isn't a one-size-fits-all maintenance strategy. The best strategy depends on the machine asset's complexity and criticality. The chart below breaks these two variables into 4 quadrants and plots where each maintenance strategy aligns best for that type of machine.

- Simpler and Not-Very Critical Assets may get away with a reactive strategy depending on how easy they are to repair and how inexpensive downtime costs. But as either the complexity to repair or the criticality of the asset increases, a preventative maintenance strategy will be the most cost effective.
- Simpler Yet Critical Assets will benefit most from a condition-based maintenance strategy to prevent downtime while being effective at detecting failure of the simpler machine. Prime examples of these machine types are bearings that operate at generally one speed and pumps.
- Complex & Critical Assets will benefit most from predictive or prescriptive maintenance. More complex machines require more than just one variable to monitor and the ability to understand different operating states and what is "good" and "bad" signatures in those varying states. And the improved analytics will enable even less downtime of your critical asset to keep it running and generating money!
- Complex Yet Not-Very Critical Assets don't really have a good fit. It depends on just how expensive it is to repair a catastrophic failure. It is unlikely that CBM will work for these type of assets, though, because operating conditions will require many variables to be monitored and analyzed. High repair costs may warrant predictive or prescriptive maintenance, but low repair costs may allow some preventive maintenance, or even reactive maintenance, to make sense.
How to Get Started with Prescriptive Maintenance - Explore!
Hopefully the benefits of prescriptive maintenance are intriguing, but how do you get started!? Well, you can't start off by doing prescriptive maintenance -- you can't even start off by doing predictive maintenance. The way you get started is by getting some data on your machine at a few different times.
Ideally, you are already doing some preventative maintenance and so you are utilizing a schedule to go out to the asset, inspect it, and potentially repair parts. Use these opportunities to gather some vibration, temperature, and other sensor data on your asset.
You don't have to use a fancy wireless monitoring system for this, either. You can use a simple vibration meter or data logger (See our blog post 6 Ways to Measure Vibration for an explanation of the full range of vibration measurement systems readily available to a test engineer).
As you go through the process of collecting data on your asset, you will be able to determine:
- How accessible is your asset for sensors?
- What type of vibration signature is present in the asset? Does it look erratic or steady from one test to the next?
- What metrics seem to show some valuable insight? Do you need to be looking in the frequency spectrum or just simply the velocity RMS?
Once you're able to answer these questions, you'll be able to understand if a data-driven maintenance strategy can work for you and your machines. Then you can begin expanding your "exploration" period. This data-driven maintenance exploration will eventually evolve into a prescriptive maintenance strategy over the course of time with continuous data collection and data analysis.
Like I demonstrated earlier with the maintenance evolution chart, prescriptive maintenance requires an evolution. All you have to do to start the process is start taking some data!
Conclusion and Additional Resources
I hope that after reading this post that you now have a good understanding of the differences between reactive, preventative, condition-based, predictive, and prescriptive maintenance and that you're ready to start collecting some data and exploring how you can perform prescriptive maintenance on your own assets.
If you have any questions, please don't hesitate to leave a comment or contact us directly. We are here to help you with all your testing and analysis needs! And, if you liked this post, I hope you'll subscribe to our blog for monthly updates on monitoring, vibration analysis, data acquisition and more!
Related Posts:
- Top 9 Accurate Wireless Vibration Monitoring Systems
- Top 12 Vibration Metrics to Monitor & How to Calculate Them
- Why the Power Spectral Density (PSD) is the Gold Standard of Vibration Analysis
For more on this topic, visit our dedicated Wireless Vibration Monitoring Systems resource page. There you’ll find more blog posts, case studies, webinars, software, and products focused on your condition monitoring and maintenance needs.