Vibration measurement isn't always a straightforward task. Not only are there many different instrumentation and software options you must choose from, finding vetted suppliers can be a task in of itself.
In this post, I'll list and explain the common sensor types and systems used to measure vibration. When I can, I'll also provide links to suppliers online where you can purchase these sensors (although some companies still require you to request a quote - stupid I know). For each sensor type, we'll start off with a list of suppliers and the pros and cons before diving into more detail.
I know you're short on time, so I've started the post with a summary table of the sensor options I'll cover. At the end of the post will be additional resources if you need further help in your vibration testing!
Sensor Type | When to Use | When not to Use | Top Supplier |
Accelerometer | General purpose shock and vibration | Limited budget and access to necessary electronics | PCB Piezotronics |
Strain Gauge | Curved surfaces, when size and mass are important, need strain data | Time or wiring constraints, need to measure acceleration | HBM |
Velocity Sensor | High temperature (> 700 °F) applications | Hard to find, generally better to use accelerometer and integrate | |
Gyroscope | Orientation data is required | Typically not used on their own, but with accelerometer | Analog Devices |
Microphone or Pressure | Health monitoring, determine vibration frequency | To measure acceleration directly, determine vibration at known locations | PCB Piezotronics |
Laser Displacement | Measure displacement directly without altering your structure or product | Outside of the lab, when power is a concern | KEYENCE |
Eddy Current or Capacitive Displacement | Measure displacement directly without altering your structure or product | Outside of the lab, when power is a concern | Lion Precision |
Vibration Meter | Quick go/no-go diagnosis of machinery | Transient events and longer than 15-second tests | Fluke |
Vibration Data Logger | Save time & cost, testing in the field (portability important) | Modal testing, very fast sampling needed (> 20 kHz) | enDAQ (a division of Mide Technology) |
Contact Vibration Sensors
The following sensors require mounting the transducer to the vibrating test piece. This has the advantage of moving with the test article to measure absolute motion, but this requires a slight modification to the vibration environment (adding mass can change the mode shapes and frequencies). Also, pay special attention to mounting the sensor. In order to accurately measure the motion, a good coupling must be achieved between the sensor and the test article - mounting matters a lot!
Accelerometer
Accelerometer Suppliers | Accelerometer Pros | Accelerometer Cons |
|
|
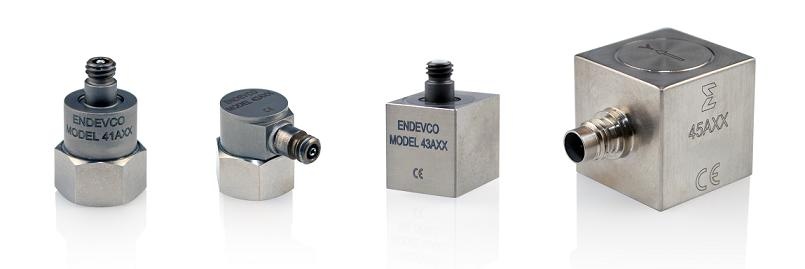
Figure 1: Accelerometers are the most common sensor type for vibration testing. [Image Source]
By far the most popular vibration sensor type is an accelerometer. As the name implies, accelerometers measure acceleration levels which are generally reported with the symbol g (equal to the acceleration of gravity, 9.81 m/s2 or 32.2 ft/s2). For some applications you may be more interested in the velocity or displacement than in absolute acceleration levels, but this can be calculated by integrating the acceleration data. For periodic motion, this integration can be very accurate but for transient events like shocks, this can lead to run-away integration error. Therefore it's best to do integrations for small time segments where the vibration is very periodic to calculate the velocity and displacement data.
There are three main types of accelerometers: piezoelectric, piezoresistive, and capacitive MEMS. The working principle of these are all slightly different and therefore the best applications for each accelerometer type is different.
Piezoelectric Accelerometer
Piezoelectric accelerometers are the most popular for their wide availability and high signal-to-noise ratio. They are AC coupled though so they can't measure static accelerations like gravity. They can also experience issues when excited at their internal resonance. They are typically between $300 and $3,000 per axis.
Piezoresistive Accelerometer
Piezoresistive accelerometers are becoming increasingly popular because they overcome the issues a piezoelectric accelerometer experiences at high (internal damping and don't magnify resonance issues) and low frequencies (measure down to 0 Hz). But they are typically 2 to 5 times more expensive than piezoelectric accelerometers.
Capacitive MEMS
These are the type you'll find in your phone. Capacitive MEMS accelerometers are the most cost-effective accelerometers (down to <$10 price range) and are typically PCB board mounted. Their data quality is typically much noisier than piezoelectric accelerometers and limited to bandwidths below a few hundred Hertz. But the quality is improving and for many general purpose applications, the data quality is plenty good enough.
Strain Gauges
Strain Gauge Suppliers | Strain Gauge Pros | Strain Gauge Cons |
|
|
|
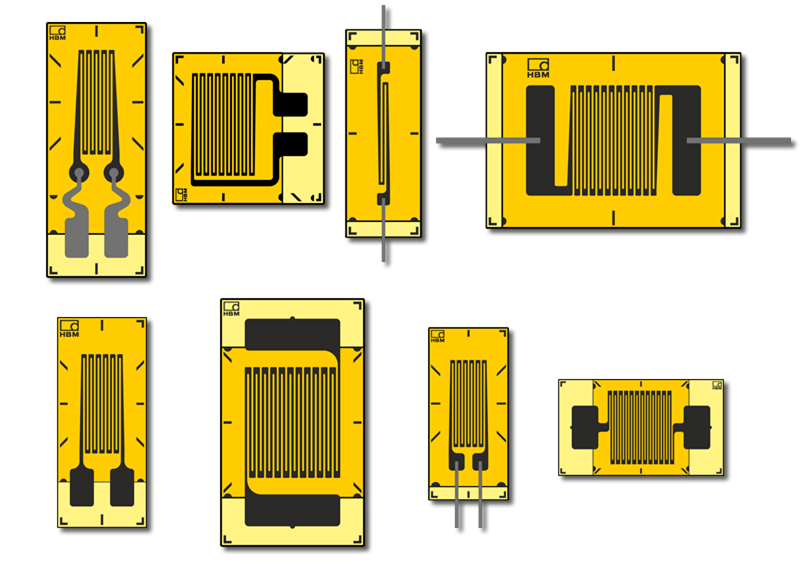
Figure 2: Strain gauges are popular for directly measuring strain. [Image Source]
How does a strain gauge work?
A strain gauge is a foil with an electrically conductive grid. As a strain gauge is stretched or compressed, the electrical resistance of the grid increases or decreases proportionally. The reason being that as the grid is stretched, the current has to travel a greater distance in a thinner conductor which both lead to increased resistance (and vice versa).
Why use a strain gauge for vibration measurement?
For more on how strain gauges work, check out HBM's article; but what makes them a good, and bad, sensor for measuring vibration? The good is that they are very versatile and accurate. They can be installed on virtually any surface and shape, and they measure both static and dynamic loads. They also measure strain directly so that calculating the stress in the material is fairly easy and accurate.
Strain gauges are also very small, and lightweight. So they don't really alter the overall stiffness of the test specimen. And best of all, a typical strain gauge will cost only a few dollars to a few hundred for very high-quality ones. What's not to love?!
Why wouldn't you use a strain gauge for vibration measurement?
They are a pain in the butt to install!
Take a look at a popular strain gauge installation tutorial - it's 20 minutes long to install these properly when you know what you're doing. I remember an intern at Mide many years ago exclaiming to me that he had successfully made a removable strain gauge - he just used double sided tape to apply it!... that obviously won't adequately adhere the strain gauge to the material. Mounting accelerometers are important but they just need to accelerate with the test instrument. For strain gauges, they need to be perfectly bonded to the material across the entire face to strain with the test article.
The other challenge strain gauges pose is that the electronics necessary to amplify the signal and acquire the data are costly (upwards of $10K), and cumbersome.
Strain gauges are awesome if you know what you're doing and have all the right equipment. But if you're reading this blog post, you likely aren't an expert in vibration testing and therefore I'd recommend steering clear of using strain gauges.
Electromagnetic Velocity Sensor
Velocity Sensor Suppliers | Velocity Sensor Pros | Velocity Sensor Cons |
|
|
|
I almost didn't include these in the list, but I know you may run across mention of them in your search for vibration sensor options. They operate by using the current generated from a magnet traveling within a coil. The advantage of these is that they measure velocity directly and they have a very high-temperature range.
But over the last 5 to 10 years piezoelectric accelerometers have improved in regard to noise, size, and durability. So now virtually everyone (except the energy industry in super hot applications) uses accelerometers and integrate the output to calculate velocity. For more on the relationship between acceleration, velocity, and displacement - check out our simple harmonic motion calculator.
Gyroscope (Angular Rate Sensor)
Gyroscope Suppliers | Gyroscope Pros | Gyroscope Cons |
|
|
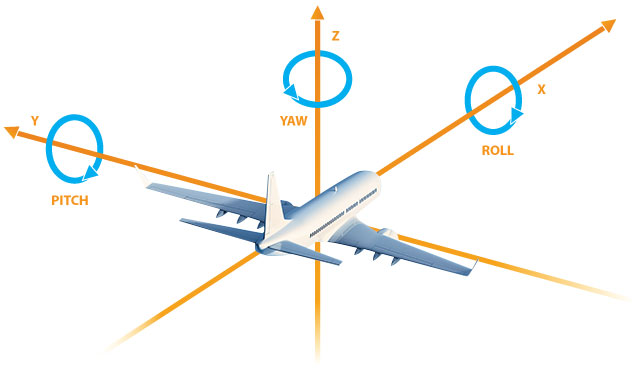
Figure 3: Gyroscopes, when used with accelerometers, provide absolute orientation information during a vibration test.
Where accelerometers measure linear acceleration, gyroscopes measure angular rate. Instead of an output in gs we get a rate value, typically displayed as degrees per second (°/s).
How does a gyroscope work?
Most gyroscopes now use MEMS technology and have three small resonating masses that get shifted as the angular velocity changes, utilizing the Coriolis effect. A much more detailed description is available from Analog Devices.
Why is a gyroscope helpful for vibration testing?
Gyroscopes provide a frame of reference one doesn't have with an accelerometer alone (or even a bunch of accelerometers). Accelerometers measure inertial forces, so yes they can help provide a frame of reference in relation to gravity, but it gets messy (and near impossible) to keep that reference when your accelerometer is vibrating itself... which will typically be the case when doing vibration testing. An accelerometer can also get "disoriented" during events that have sustained static accelerations (like a banking aircraft) that can be misinterpreted as the gravity vector. The gyroscope, however, would allow the system to know the true course of motion.
Gyroscopes, when used in conjunction with accelerometers, help keep track of the orientation of your system. One wouldn't typically use a gyroscope alone for vibration testing but with accelerometers, you'll have a much more complete picture of the vibrating environment.
Non-Contact Vibration Sensors
enDAQ makes vibration data loggers (formerly known as Slam Sticks) that we market as easy-to-use, yet accurate and high quality, alternatives to traditional vibration measurement systems. In a moment of brilliance, a not-so-technical coworker of mine exclaimed that we could make it really easy to measure vibration if we can figure out a way to "measure vibration through the air!"
My first reaction was to suggest that "measuring vibration through the air" is impossible - in order to measure vibration, the sensor (or sensing system) needs to be mechanically attached to vibrate along with the test structure or device. But that is not actually the case...
Microphones or Acoustic Pressure Sensors
Microphone Suppliers | Microphone Pros | Microphone Cons |
|
|
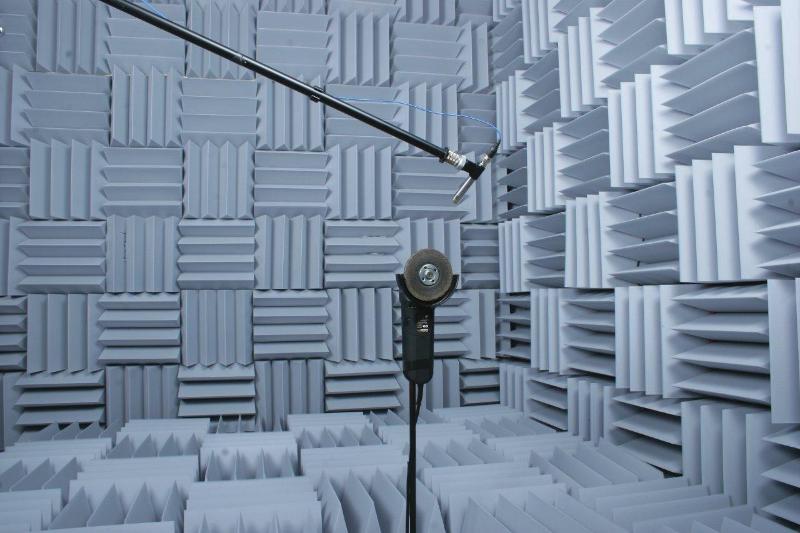
Sound is not often thought of as a way to measure vibration, but it should be! After all sound, by definition, is a vibration that travels through the air in the form of pressure waves.
When to use a microphone or pressure sensor for vibration testing?
Microphones offer a cost-effective means of measuring high-frequency vibration and is especially useful to determine how a system’s vibration changes with time. Health monitoring applications can greatly benefit from using a microphone on cost and simplicity. Microphones can also provide a very clear and accurate representation of the frequency content in your vibration.
Microphones aren’t limited to applications where cost is a concern; some acoustics applications will use high-end microphones for vibration testing and analysis. You’ll notice a lot of the accelerometer companies also offering high-end microphones. Acoustics is a major area of vibration testing and has very similar analysis, data acquisition, and sensor characteristics.
When not to use a microphone for vibration testing?
Microphones and acoustic analysis can be a great option for some applications; but if you need absolute shock and vibration data, not relative change, then microphones probably won’t work. They also won’t be able to analyze modal shapes and specific/discrete points along your structure. But again, they are very effective for overall frequency analysis.
Laser Displacement Sensor
Laser Displacement Suppliers | Laser Displacement Pros | Laser Displacement Cons |
|
|
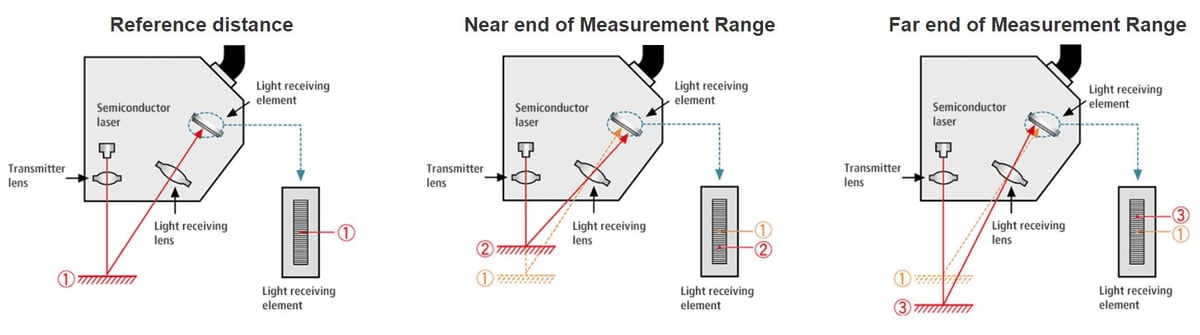
Figure 5: Laser displacement sensors measure the distance between itself and a target - helpful for some vibration testing applications. [Image Source]
How does a laser displacement sensor work?
A laser displacement sensor uses triangulation with a transmitting and receiving lens. A laser beam is emitted down towards the target through a transmitting lens. The light then reflects back towards the sensor and is directed by a receiver lens to a receiving element. As the target moves closer and farther away, the angle of the reflected light changes (it's focused on a different position on the receiving element).
When using a laser displacement sensor makes sense?
Displacement sensors can be preferred in some applications that prevent the use of accelerometers such as rotating components (although a data logger could be used), or when the accelerometer’s mass would too greatly influence the motion of the system. They also measure displacement directly which may be the true parameter of interest (not gs) for certain vibration testing applications.
When to avoid laser displacement sensors?
The downside to using these is that it’s measuring relative motion between two structures. These are near impossible to use in the field because a fixed mounting and distance is required between the sensor and equilibrium position of the vibrating structure. They can also be quite a bit more expensive (system cost over $5K) and complex than accelerometer-based systems. Also, displacement sensors should be avoided for shock testing for fear of damaging the sensors.
Eddy Current and Capacitive Displacement Sensors
Displacement Sensor Suppliers | Displacement Sensor Pros | Displacement Sensor Cons |
|
|
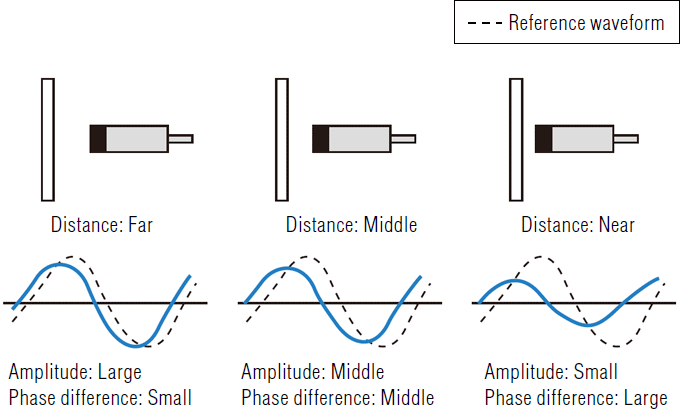
Figure 6: Eddy current and capacitive displacement sensors measure the distance between itself and a target - helpful for some vibration testing applications. [Image Source]
These sensors have similar benefits and drawbacks as lasers for vibration testing. On the one hand, they offer a way to "measure vibration through the air" without altering your vibrating system. But they only measure relative motion, they need to remain fixed and measure the difference in motion of a nearby structure. So they typically are used only in the lab especially considering the fragility of the system (expensive sensors, wiring concerns, and power supplies).
Difference between eddy-current and capacitive displacement sensors?
Lion Precision does a much deeper comparison between the two sensor types than I could ever that's worth checking out if you're interested. But to summarize, capacitive sensors use a high-intensity electric field it generates. So long as the material of the target doesn't change, the only dynamic variable that impacts the strength of the reflected field is the distance between the target. Similarly, an eddy-current sensor creates a magnetic field and measures the changing response of that field.
Vibration Sensing Systems
All the previous vibration sensor options discussed require the user to handle wiring, provide power, signal conditioning, and electronics to acquire the data. The next two options do all that for you in one, self-contained system. These make it much easier to do vibration testing for the general purpose user, but they often come in handy for advanced vibration measurement and analysis experts for initial testing.
Vibration Meters
Vibration Meter Suppliers | Vibration Meter Pros | Vibration Meter Cons |
|
|
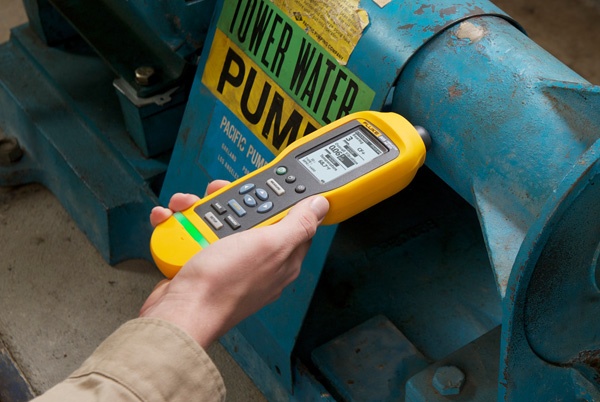
Figure 7: Vibration meters are a tool that enable you to get a quick overview of the vibration environment. [Image Source]
Vibration meters offer real-time vibration analysis in a handheld unit so that maintenance decisions can be made quickly in the field. They either wire to a traditional accelerometer or some even incorporate the accelerometer into the unit cutting down on wiring requirements and complexity. Vibration meters give RMS and peak-to-peak levels in real time, sometimes include the resonant frequency of the vibration. They also will typically have an algorithm to rate the overall vibration of your bearing or machine.
When to use a vibration meter?
Vibration meters are typically used in industrial health monitoring. A technician will routinely (fixed schedule or when he/she suspects a problem) inspect the machinery. The setup is very quick: just press the device to the machine (if it has the embedded accelerometer), read the vibration level and then make a decision if maintenance or repair is needed. For that quick go/no-go vibration testing of a piece of machinery, a vibration meter is unbeatable.
When not to use a vibration meter?
Vibration meters don’t allow the user to log long duration events (they may give you access to the last couple thousand points for some analysis). Vibration meters can also be a bit pricey at around $1,000 which typically won’t include the cost of the accelerometer (the Fluke 805 is over $2K that has the embedded accelerometer). If you are looking to do some more in-depth vibration analysis or any shock testing, a vibration meter is probably not your best option.
Vibration Data Loggers
Vibration Recorder Suppliers | Vibration Recorder Pros | Vibration Recorder Cons |
|
|
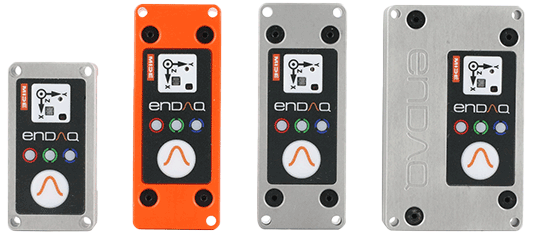
Figure 8: Vibration data loggers offer a cost effective way to capture vibration data quickly and easily. They are often used before setting up more complex systems and for some applications completely replace the "traditional" wired accelerometer based setup.
Vibration data loggers combine all the components necessary for most entry to mid-level vibration testing applications:
- Embedded accelerometer(s)
- Data acquisition and storage
- Power with embedded battery
- Signal processing and filtering (hopefully)
For a detailed list of vibration data logger options and a comparison of them (including our competitors) check out our post: Rating My Top 11 Vibration Data Loggers.
When to use a vibration data logger?
To put it simply - vibration data loggers are when you grimace at the complexity and cost of setting up a "traditional" accelerometer-based vibration measurement system.
Vibration data loggers are best for applications that need to do some testing quickly. They are very easy to set up (just tape or bolt to surface and press the button) so that an engineer (but you don't need to be all that technical) is able to acquire vibration data quickly and easily. Everything is self-contained so vibration data loggers are also extremely portable - making testing in the field very easy.
A typical use case for a vibration data logger is when you are designing a product or system and need to get some test data from its intended operational environment (not all this data is readily accessible). For this application, you can set up the test, leave it for minutes or hours, then return to download the data and see what type of vibration and shock events occurred.
One can also use a vibration data logger when wiring is not feasible. This includes some ammunition testing (we've had customers put enDAQ sensors in missiles - hopefully they retrieved them and the data!), rotating machinery, the outside of an aircraft (one customer that I know about even flew with the sensor mounted to the wing with a bunch of duct sealing), etc.
Lastly, vibration data loggers are a good tool to use before setting up more complicated systems. We often have vibration analysts send a vibration data logger to a client to perform some initial testing before they need to travel to the location themselves. The initial testing will help provide some information on the type of environment so that appropriate advanced sensors can be used, and it may even help locate key areas to mount those sensors.
When to not use a vibration data logger?
Vibration data loggers are limited in two main areas: lack of synchronization, and a (generally) poorer data quality. Because it's difficult to synchronize between units you won't be able to do modal testing of large structures. That doesn't mean that vibration data loggers aren't time-stamped; they are. But the time stamp isn't accurate enough (typically 100s of milliseconds when you may need less than a millisecond precision).
Vibration data loggers are also often thought of as having poor data quality. While that may be true for systems made over 10 years ago, sensing technology is improving and getting smaller. Not to mention, embedded electronics are also becoming increasingly more capable of performing the high-speed processing and data acquisition necessary.
That being said, sampling rates will be limited to 20,000 Hz for higher end data loggers and the noise floor will typically be higher compared to an advanced accelerometer.
Summary
If you're still reading this post, hopefully, you have a better idea of which sensor is best for your application! If not, don't hesitate to reach out to us and ask. And here's that summary comparison table again for reference.
Sensor Type | When to Use | When not to Use | Top Supplier |
Accelerometer | General purpose shock and vibration | Limited budget and access to necessary electronics | PCB Piezotronics |
Strain Gauge | Curved surfaces, when size and mass are important, need strain data | Time or wiring constraints, need to measure acceleration | HBM |
Velocity Sensor | High temperature (> 700 °F) applications | Hard to find, generally better to use accelerometer and integrate | |
Gyroscope | Orientation data is required | Typically not used on their own, but with accelerometer | Analog Devices |
Microphone or Pressure | Health monitoring, determine vibration frequency | To measure acceleration directly, determine vibration at known locations | PCB Piezotronics |
Laser Displacement | Measure displacement directly without altering your structure or product | Outside of the lab, when power is a concern | KEYENCE |
Eddy Current or Capacitive Displacement | Measure displacement directly without altering your structure or product | Outside of the lab, when power is a concern | Lion Precision |
Vibration Meter | Quick go/no-go diagnosis of machinery | Transient events and longer than 15-second tests | Fluke |
Vibration Data Logger | Save time & cost, testing in the field (portability important) | Modal testing, very fast sampling needed (> 20 kHz) | enDAQ |
Additional Resources
If you'd like to learn a little more about various aspects in shock and vibration testing and analysis, download our free Shock & Vibration Testing Overview eBook. In there are some examples, background, and a ton of links to where you can learn more.
Related Posts:
- Vibration Measurements: Vibration Analysis Basics
- MATLAB vs Python: Speed Test for Vibration Analysis [Free Download]
- Get Started with Python: Why and How Mechanical Engineers Should Make the Switch
For more on this topic, visit our dedicated Vibration Loggers & Vibration Sensors resource page. There you’ll find more blog posts, case studies, webinars, software, and products focused on your vibration testing and analysis needs.